3D printed gloves for rehabilitating stroke patients
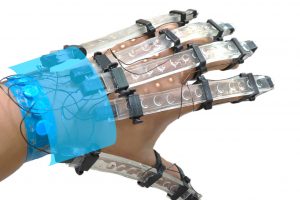
Stroke is India’s third leading cause of death and the sixth leading cause of disability. Physiotherapy is one of the few treatments available for rehabilitating stroke victims and patients with physical injuries. However, physiotherapy can take days to months depending on the severity of the disability, making it challenging for patients as well as their attendants.
To help these patients, researchers in the Department of Physics at the Indian Institute of Science (IISc) have developed a soft, wearable device that exploits the fundamental properties of light to sense a patient’s limb or finger movements. The customizable, 3D printed gloves can be remotely controlled, opening up the possibility of teleconsultation by physiotherapists.
“We wanted to develop something affordable, and available to a person at all times at their convenience. The product should be easy to use and must provide feedback,” says Aveek Bid, associate professor at the Department of Physics, whose team has developed the device.
Bid explains that quantifiable feedback—for example, the units of pressure applied while squeezing a ball or the degree of bending of a leg with a knee injury—is crucial for doctors to monitor the patient, even remotely. Such feedback can also motivate patients to perform better in every consecutive session.
Another challenge is that physiotherapy often requires daily hospital visits. Home visits by professionals or sophisticated devices to monitor patients remotely, although ideal, are not readily available and are expensive.
To address these challenges, the team has developed a mechanism by which customizable wearables like hand gloves can be designed, 3D printed, and controlled remotely. “The idea behind the device is that you wear something like a glove, the physiotherapist controls the device from a remote location through the internet, and makes your hands and fingers move,” describes Bid. The device can sense various hand and finger movements, and precisely detect parameters like pressure, bending angle and shape.
The technology that drives the device is based on the fundamental properties of light: refraction and reflection. A light source is placed at one end of a transparent rubbery material, and the other end has a light detector. Any movement in the finger or arm of the patient causes the flexible material to deform. The deformation alters the path of light, and thereby its properties. The device translates this change in light properties to a quantifiable unit. Since light travels across the entire length of the device, movement along any part of the patient’s finger or arm can be accurately measured.
The device is highly sensitive—enough to respond to the touch of a butterfly, says team member Abhijit Chandra Roy, DST-Inspire Faculty at the Department of Physics and the brains behind the project. In addition, while existing devices can only detect the bending of a finger, the new device can even measure the degree of bending at every joint of the finger, he explains.
For their device, the researchers used a silicon-based polymer material that is transparent (facilitating manipulation of light), soft (for comfort and repeated use), and most importantly, 3D printed; it can therefore be customized to fit each patient’s arm and fingers. The device can also capture and store data, and transmit it over the internet, facilitating remote monitoring by clinicians or physiotherapists.
Source: Read Full Article